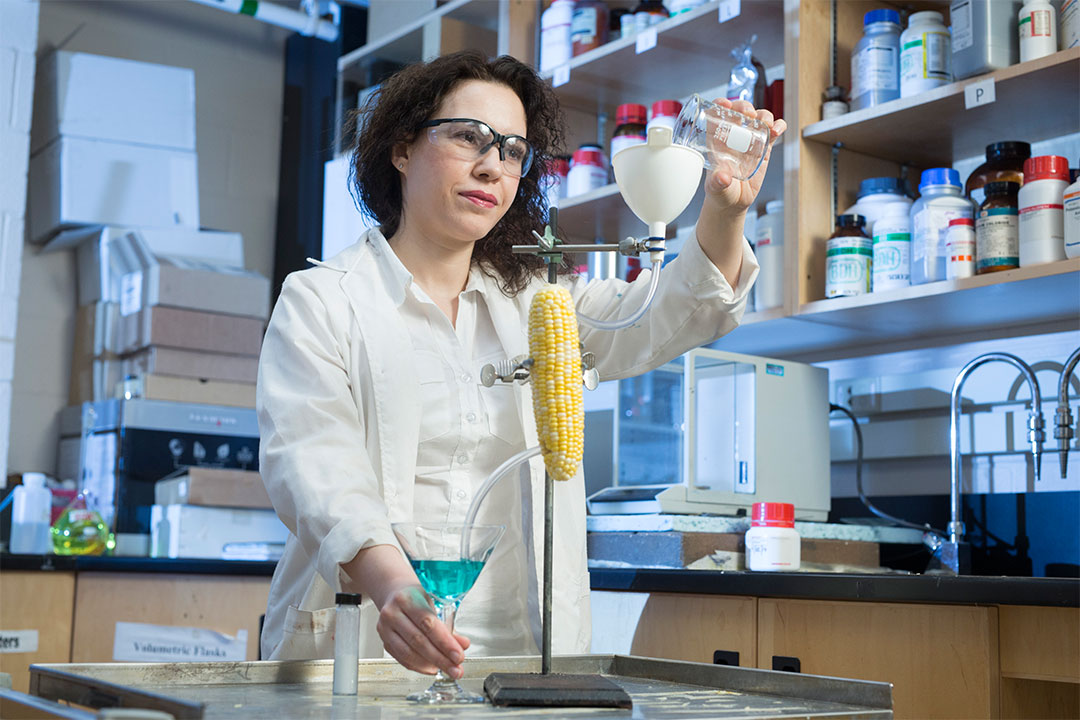
Developing new technology for cheaper biofuel
New University of Saskatchewan chemistry research could pave the way for cheaper gas and booze.
By Federica GiannelliPhD chemistry student Leila Dehabadi has developed a new way to separate water from ethanol, the key component in alcoholic beverages and biofuel, using starch-based materials such as corn. The method could reduce costs because it doesn’t involve using additional energy to isolate the ethanol.
“Compared to distillation, this new approach based on green chemistry and engineering will be a significant saving to biofuel and alcohol production in Saskatchewan and globally by changing the way water is separated from ethanol mixtures,” said Lee Wilson, U of S chemistry professor and Dehabadi’s supervisor.
In traditional distillation methods, fermented plants create a mixture of water and ethanol which is then heated to separate out the ethanol. However, some water remains, Dehabadi said.
She solved this problem by using non-toxic starch-based materials that do not require energy to remove water. Published in ACS Sustainable Chemistry & Engineering in 2016 and 2017, her results show the new technology is 40 times more effective than materials previously studied and achieves an efficiency comparable to traditional distillation.
Dehabadi has modified different types of starch (corn) and cellulose (plants) to create materials with varying chemical compositions and textural properties.
During trials, she found that her materials act like “selective sponges,” and remove water better than cellulose-based ones.
When immersed in a mixture of water and ethanol, her new materials suck up 80 times more water than ethanol.
“You can repeat the process in a ‘loop’ to get more ethanol,” said Wilson.
Present in staple foods such as corn, potatoes and cereals, starch makes these new materials inexpensive to produce. They are also easily “tunable” which means companies would be able to adjust the materials’ water removal ability based on specific production needs.
“If all goes well with the research, I hope to commercialize our starch-based materials in 5 years,” said Wilson.
In collaboration with the U of S College of Engineering, Wilson and Dehabadi have also been testing these starch-based materials for use in a new class of air conditioning systems.
“The materials can be used in these systems to remove moisture and humidity more efficiently,” said Dehabadi, who receives funding from the Saskatchewan Agriculture Development Fund.
Dehabadi’s published results have shown her materials remove moisture 13 per cent more efficiently than products currently available on the market. Dehabadi and Wilson will focus on improving this application as their next research step.
Dehabadi chose to come to the U of S from Iran because of the university’s expertise in biofuels and bio-energy from animal and agricultural waste and because of her desire to work on research projects with applications in industry.
“My friends who attended the U of S talked highly about the lab facilities, high standard of education and possibilities of having a good career after graduating,” she said.
Federica Giannelli is a graduate student intern in the U of S research profile and impact unit.
This article first ran as part of the 2017 Young Innovators series, an initiative of the U of S Research Profile and Impact office in partnership with the Saskatoon StarPhoenix.