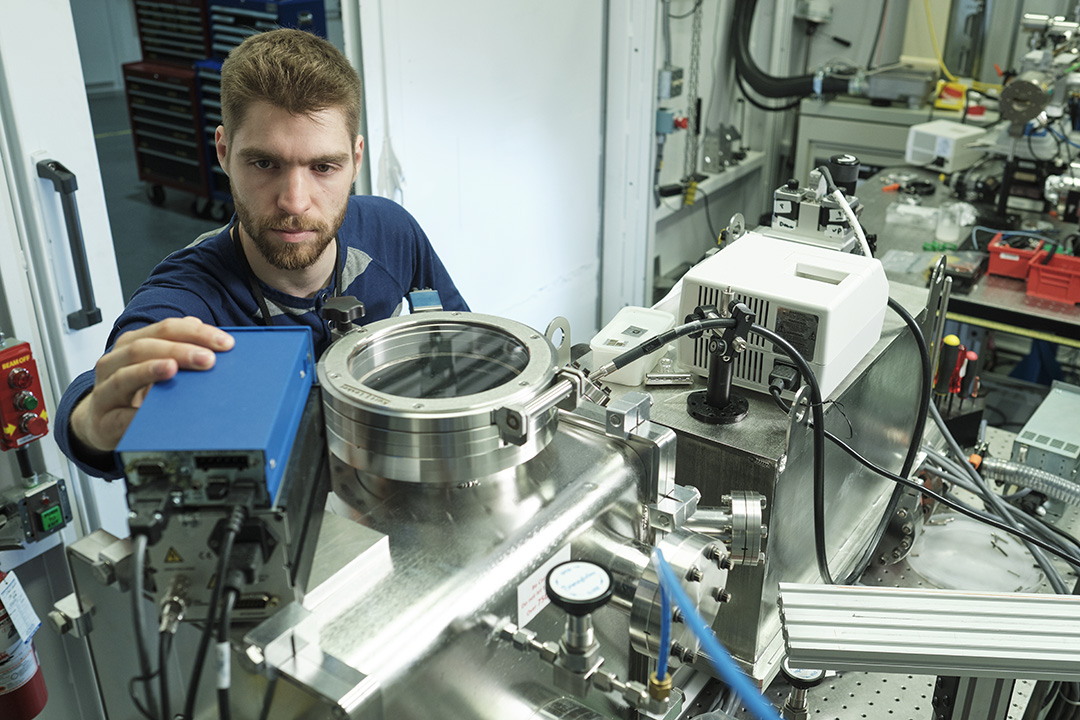
New technique for studying rusting of steel benefits mining industry
University of Saskatchewan (USask) PhD student Arthur Situm has developed a new non-invasive technique to study the rusting of steel, research that may help with the safety of potash mining and construction of buildings, roads and bridges.
By Federica GiannelliAt the Canadian Light Source (CLS) synchrotron, a national research facility of USask, Situm has been studying how the protective coatings of rebars—the steel reinforcing bars used to strengthen concrete —withstand rusting (corrosion). He did his research with the potash mining industry especially in mind.
Salt from potash mining seeps through the porous concrete and may cause rebar to rust faster, which could require more frequent replacements. The world’s largest reserves of potash, mainly used for crop fertilizer, are in Saskatchewan and the industry is integral to the provincial economy, making up nearly 30 per cent of the mineral’s worldwide production in 2017.
“Concrete usually holds up pretty well even when the rebar is somewhat rusted, but the method I developed helps you determine at which point the protective coatings of the rebars fail, so that researchers can develop better coatings,” said Situm.
Unlike other methods used to study corrosion, Situm’s new synchrotron technique, which stems from a combination of X-rays, a microscope and the CLS particle accelerator, shows how effective the coatings are without removing them from the rebars. Normally, coating removal damages samples by making them unusable for future testing and may interfere with the corrosion of the coating itself.
The project is funded by: the federal agency NSERC; the International Minerals Innovation Institute (IMII); potash companies Nutrien, BHP and Mosaic; and Mitacs, a national not-for-profit organization that fosters growth and innovation for business and academia in Canada.
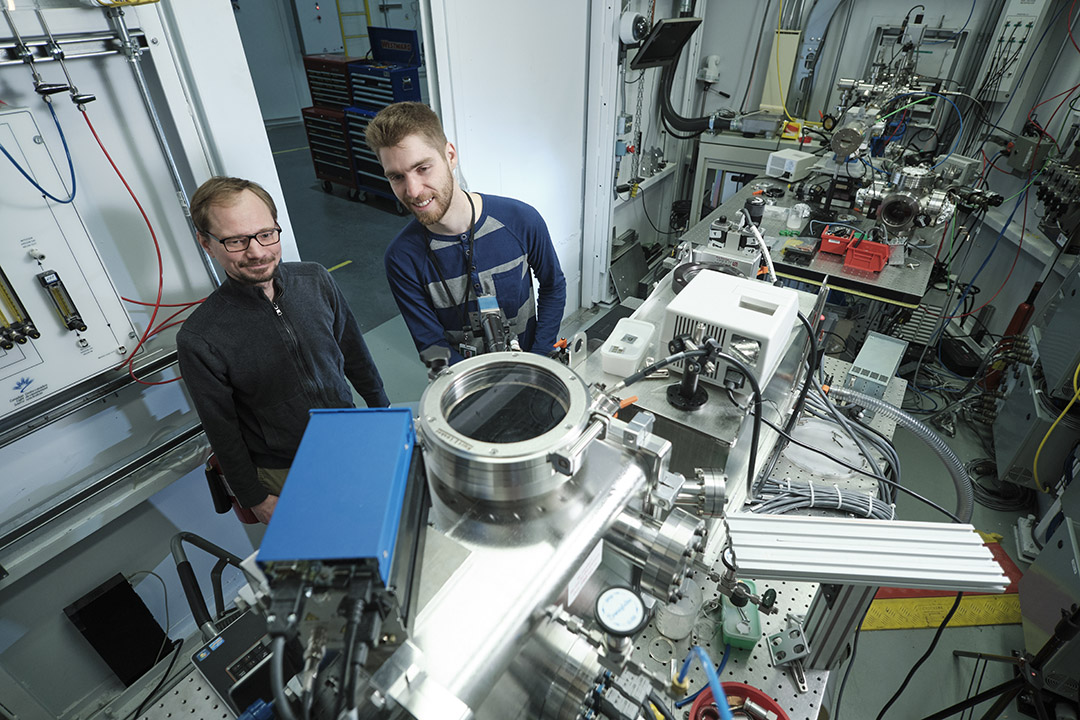
“We work closely with these companies to better understand what their needs are in terms of rebar, and we regularly share our results with them and IMII,” said chemistry professor Andrew Grosvenor, Situm’s supervisor. “We hope that by the end of the project our work will be useful for them to further improve the safety of constructions in the potash industry.”
Situm has simulated different conditions for multiple types of protective coatings in the lab to understand how the materials and surface chemicals can respond. His results show that a well-known and more expensive coating called “fusion-bonded epoxy” is able to withstand corrosion better than other types of coatings tested.
“It’s not just the work we do in the lab that can tell us to choose a particular coating. A material performance can change greatly based on the lifetime of the material and environmental exposure, so we are not recommending one coating over others,” said Grosvenor. “Arthur was more interested in finding new ways to study corrosion.”
Situm’s technique ‘maps’ how the chemical elements of a material are placed across its surface, and how they may change in response to corrosion or aging. His results are published in the journals Corrosion Science and Surface and Interface Analysis.
“Much like a map of a city, which tells you where parks and buildings are, and how big, my map shows a very accurate distribution of chemicals in a material,” he said.
Situm plans to extend the applications of his technique to study the stability of the ceramics used to store nuclear waste, using a simulated nuclear fuel.
Federica Giannelli is a graduate student intern in the University of Saskatchewan research profile and impact unit. This content runs through a partnership with The StarPhoenix.