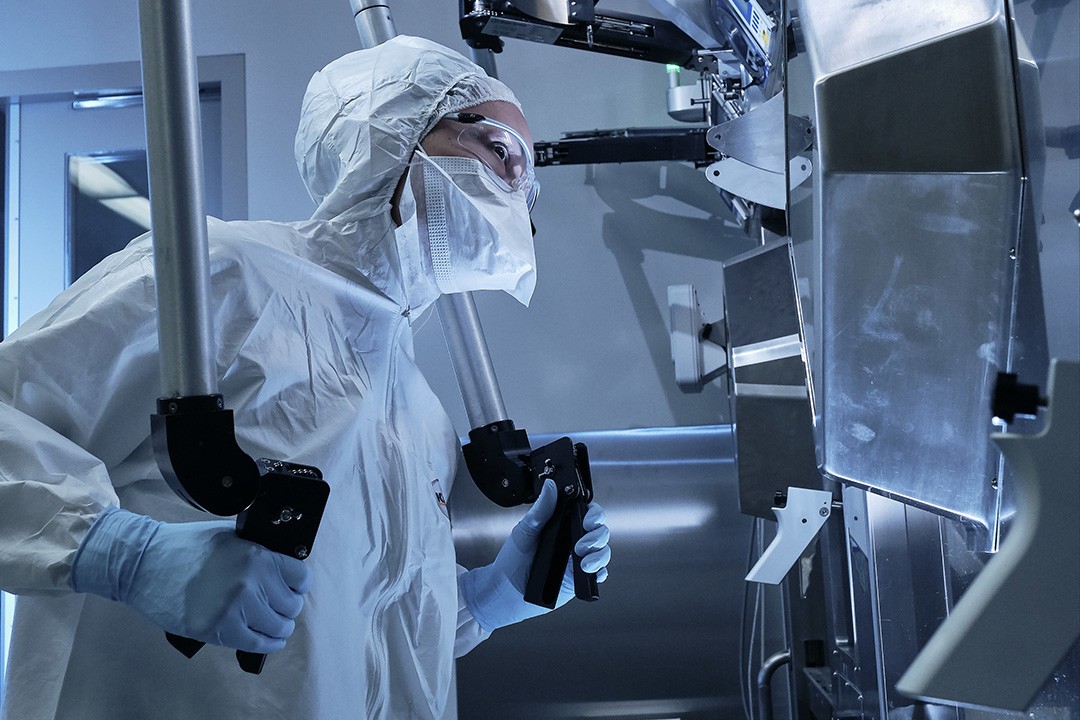
Making a difference: USask research centres help to combat COVID-19 pandemic
Several University of Saskatchewan research centres are supporting the international effort to fight COVID-19 with some of the most advanced research tools Canada has to offer.
By Kathryn WardenThe USask Vaccine and Infectious Disease Organization-International Vaccine Centre (VIDO-InterVac), one of the world’s largest and most advanced Level 3 high-containment facilities, is on the front lines of developing a vaccine to combat the pandemic.
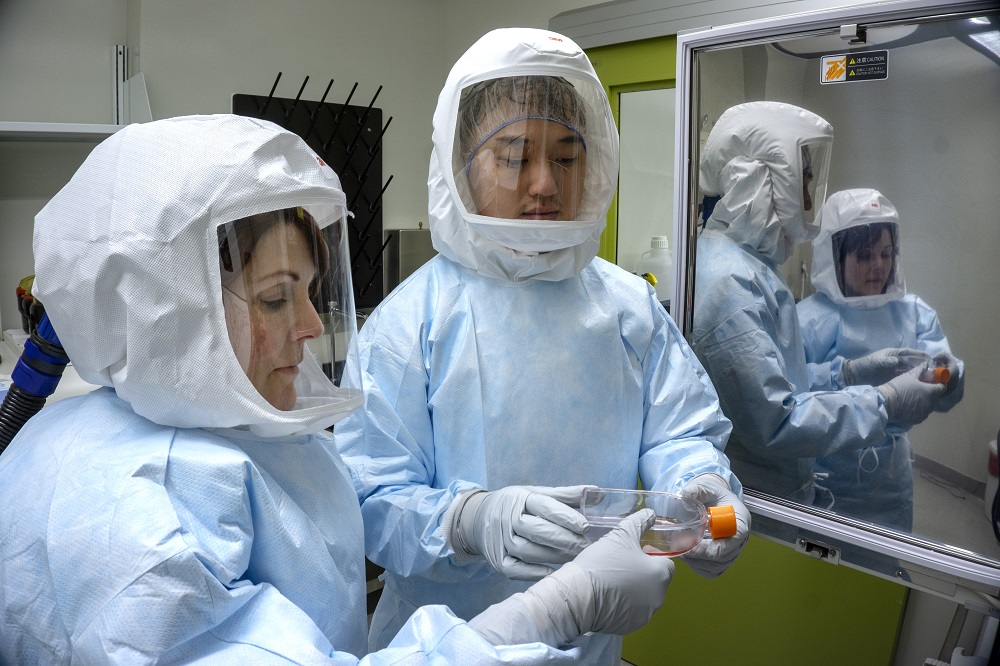
The centre’s vaccine candidate has proven highly effective in ferrets, one of the animal models VIDO-InterVac developed for COVID-19 testing. The centre hopes to move its vaccine candidate to human trials in the fall.
As well, VIDO-InterVac is testing various vaccines, antiviral medications, and novel treatments that companies around the world have developed, and has received more than 100 requests for this type of contract research. VIDO-InterVac was the first lab in Canada to isolate SARS-CoV-2 and the first in the country to establish an animal model for testing these potential medicines.
“The current coronavirus pandemic highlights why our containment Level 3 facility was built,” says VIDO-InterVac Director Volker Gerdts. “This special infrastructure enables Canadian scientists to work on diseases with high impact, such as COVID-19 and TB in humans or African Swine Fever in animals. VIDO-InterVac is part of the national and global response to such emerging disease threats.”
To make that response even faster, VIDO-InterVac is building a pilot-scale manufacturing facility that will be able to produce millions of doses of vaccines, helping to address Canada’s need for vaccine production capacity.
VIDO-InterVac is working with Saskatoon-based company ZYUS Life Sciences Inc. to see whether a plant protein can serve as a key component (an antigen) in a COVID-19 vaccine, and also with the National Research Council and other companies across Canada to accelerate development and production of an antigen from mammalian cells.
The university’s Canadian Light Source, Canada’s only synchrotron light source and an invaluable tool for innovative science in advanced materials, agriculture, environment and health, re-opened on July 21st with a focus on COVID-19-related projects.
Universities and private industry users of “Canada’s brightest light” are studying aspects of the virus’s structure to develop therapeutics that could halt the virus’s replication machinery and its spread in the body or prevent it from entering human cells to begin an infection.
CLS COVID-19-related research is focussed on three main areas:
- imaging molecular structures of the virus’s key proteins to aid drug development,
- understanding the virus’s physical behaviour and transmission including visualizing virus-carrying droplet transmission in the air, and
- improving equipment for COVID-19 frontline workers, such as microfabrication techniques for virus testing devices and studying the decomposition of N95 face respirator masks to improve decontamination and manufacturing practices.
During the pandemic, another USask research facility—the Saskatchewan Centre for Cyclotron Sciences (SCCS)—was able to ensure that Royal University Hospital could continue the essential service of PET-CT scanning for more than 600 cancer patients since early March.
With COVID-19 safety measures in place, half a dozen staff members have continued to produce and deliver nuclear-imaging agent “FDG” for PET-CT scans. These scans enable doctors to quickly and painlessly determine whether a patient has cancer, revealing the size and location of a tumour.
“So far, we have been able to maintain fully reliable delivery,” says John Root, executive director of the Sylvia Fedoruk Canadian Centre for Nuclear Innovation which operates the facility.
The SCCS supports nuclear imaging research and development by academic and industry users but suspended this work during the pandemic to further protect the isotope production staff.
“Our team is now preparing to reopen access for users, using controlled work zones and scheduling to prevent overlap with the production technologists, so that some research activities can be resumed gradually and safely,” he says.
As well, early in the pandemic, USask agriculture researchers and three local companies teamed up to address a provincial shortage of hand sanitizer using a USask bioprocessing facility to temporarily produce sanitizer and key ingredients, while the business group geared up for larger-scale production.
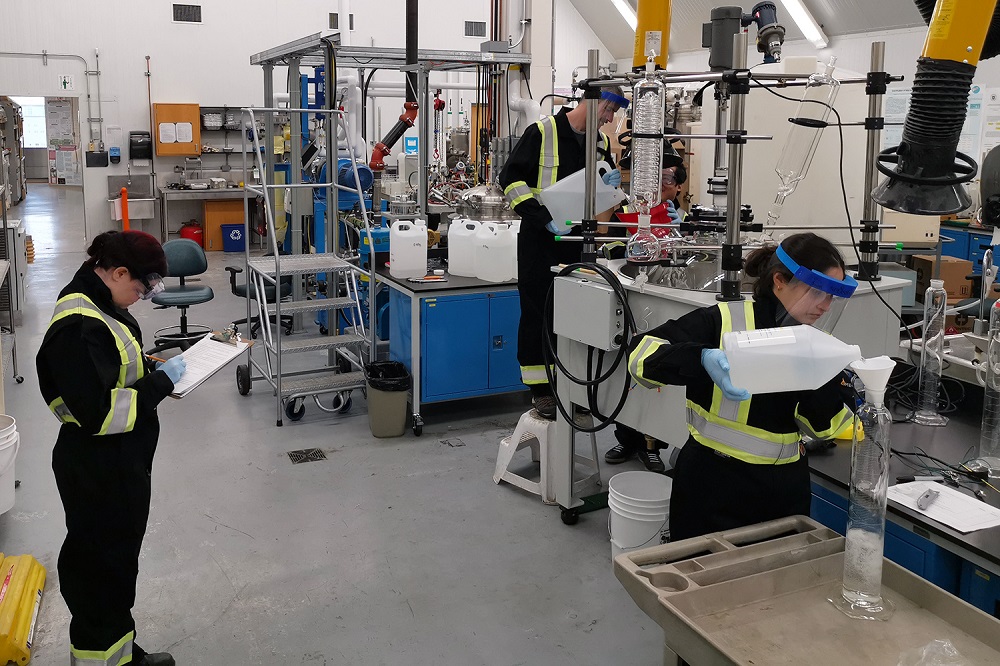
The USask Bioprocessing Pilot Plant produced up to 400 bottles a day of hand sanitizer until Bioriginal Food & Science Corp. secured a license to set up its own manufacturing facility to produce the sanitizer in larger quantities. Lanigan firm Pound-Maker Agventures Ltd., which runs an integrated feedlot and fuel ethanol facility, produced the ethanol, a key ingredient. USask spin-off Prairie Tide Diversified did the product verification analysis using the Saskatchewan Structural Sciences Centre.
Bioriginal then sold the sanitizer to the Saskatchewan Health Authority at a discounted price to help protect health-care workers, and continues to manufacture and sell hand sanitizer.
“There’s no other place where this could happen in Saskatchewan,” says USask researcher Martin Reaney. “We were able to do this at USask because of our expertise, our bioprocessing facility, and our specially equipped analytic capabilities.”