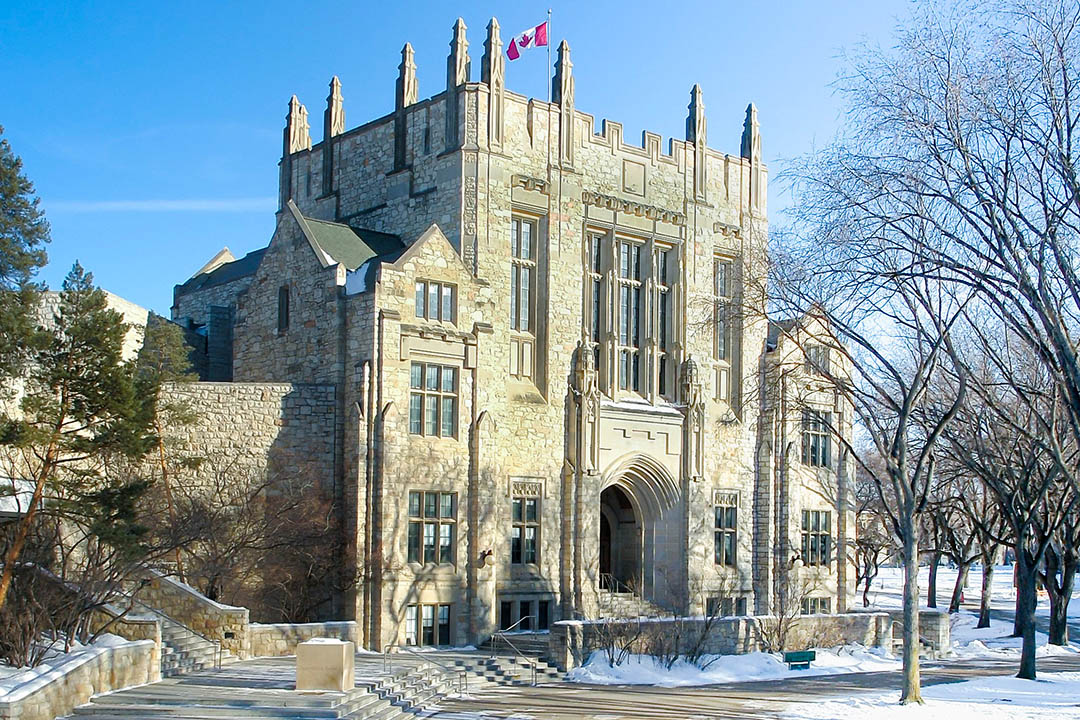
From ag waste to green energy source: USask researchers build better biomass pellet
SASKATOON – Countries in Europe and Asia are increasingly relying on biofuel – products made from wood and plant residue – as an alternative to fossil fuels in power generation and home heating. The most common form is biopellets, small, finger-sized pellets produced by compacting waste material from the forestry industry and farming.
By Greg Basky, USask Research Profile and Impact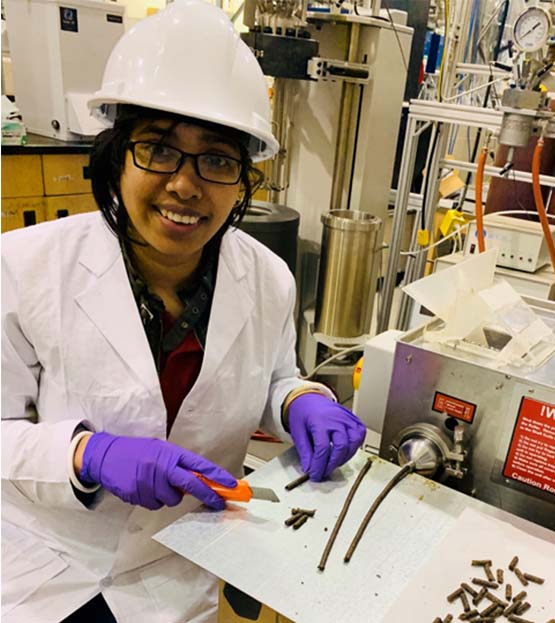
A recent discovery by researchers at the University of Saskatchewan (USask) could help hasten use of cheap and plentiful agricultural waste as the go-to material for producing this environmentally friendly energy source.
Tumpa Sarker, a PhD candidate in USask’s department of chemical and biological engineering, has found that heating canola meal, canola hull, and oat hull before compressing it yields a higher quality pellet with lower moisture content and volume, and higher energy content and density. The resulting product has a heating value similar to coal, Sarker found.
“We have all this carbon stored in forests, and plant and agricultural residue,” said Sarker. “We are looking at how to use it in place of fossil fuels to generate energy”
Many farming byproducts are currently left in the field to rot. The resulting methane releases large amounts of greenhouse gas. Compacting plant material into small pellets increases its density up to 10 times, making it much more economical to transport and store.
Canada currently exports up to 4 million tonnes of biopellets to Europe each year, the majority of which are manufactured using forestry byproducts. While some Saskatchewan companies use agricultural waste in animal feed, none are converting this material into biopellets.
“There is a really huge market for this (biofuel),” said Dr. Ajay Dalai (PhD), Sarker’s PhD supervisor and Canada Research Chair in Bio-Energy and Environmentally Friendly Chemical Processing. “The world is hungry for reducing carbon dioxide (CO2) emissions and increasing use of non-fossil fuels for generating power and heat. These pellets are a great solution. They have low net CO2 emissions. This could bring money for (agricultural) producers and generate local employment.”
The treatment process Sarker and Dalai used, called torrefaction, involves heating the biomass at temperatures between 200 and 300 degrees Celsius in an inert environment (an environment free of oxygen and CO2). Their work was done at the Catalysis and Chemical Reaction Engineering Laboratories (CCREL) in the USask College of Engineering and analyzed at USask’s Saskatchewan Structural Sciences Centre (SSSC), with testing performed using beamlines at the Canadian Light Source (CLS).
Dalai said the objective of the research – which is supported by Agriculture and Agri-food Canada as part of the Biomass Canada Cluster and by Saskatchewan’s Ministry of Agriculture – is to develop a technology that can be picked up by a local company then used to produce high-quality biopellets for energy applications.
“Europe is very aggressive in reducing their emissions,” said Dalai. “So that would be a major market if we had a local company making these pellets and exporting them abroad.”
Dalai and Sarker are now turning their attention to finding an environmentally friendly binding agent that will make the pellets more durable and more resistant to absorbing moisture during shipping.
The Saskatchewan Structural Sciences Centre (SSSC) is a $14M laboratory located in the Thorvaldson Building that university and industry scientists use for research in the fields of agriculture, medicine, engineering, and natural sciences.
-30-
For more information, contact:
Victoria Dinh
USask Media Relations
306-966-5487
victoria.dinh@usask.ca